- Reliability Edge Weekly Newsletter by Hamiltonian Systems
- Posts
- The Reliability Edge Weekly Reliability Pulse
The Reliability Edge Weekly Reliability Pulse
The newsletter for reliability and maintenance engineers and IT leaders, aiming to improve the quality of their asset and MRO data to achieve excellence in manufacturing, is published by Hamiltonian Systems. Unified data management and more...
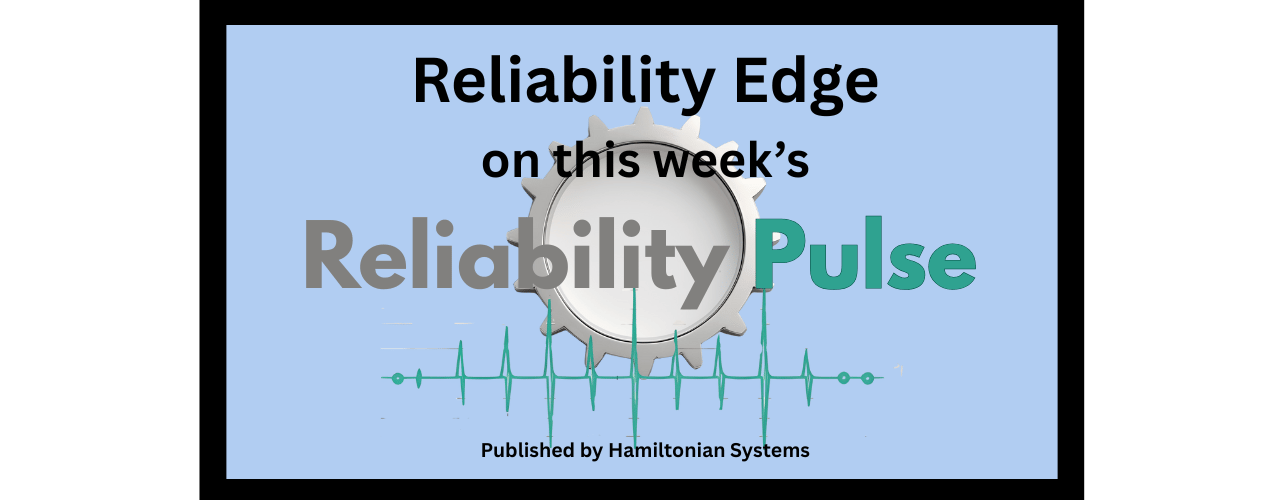
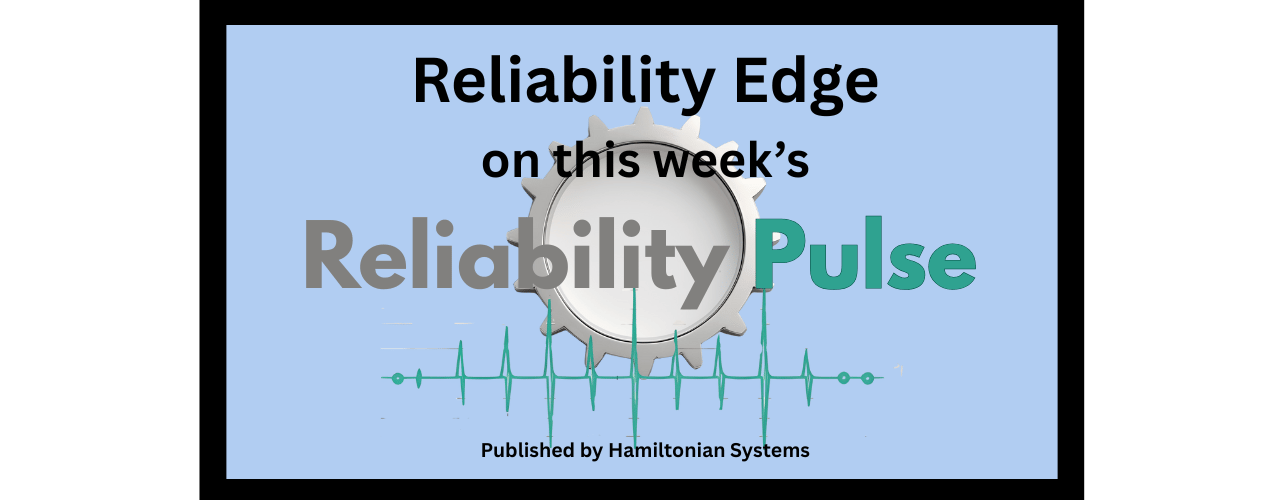
Reliability Edge on the week’s Reliability Pulse keeps you current on data, MRO & AI.

"Small improvements, consistently made, outweigh the grandest intentions.”
— Ravi Venkatraman, President of Hamiltonian Systems
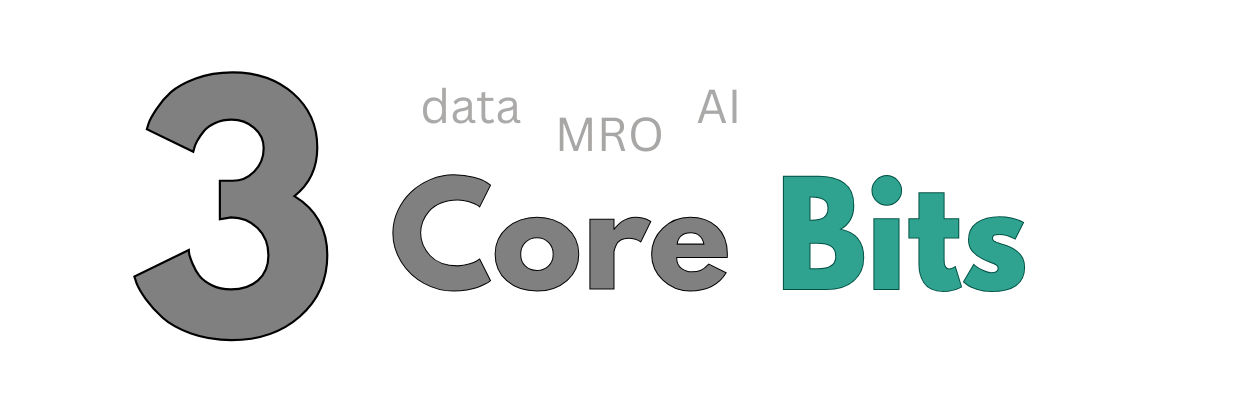
Real-time Data For Operational Stability
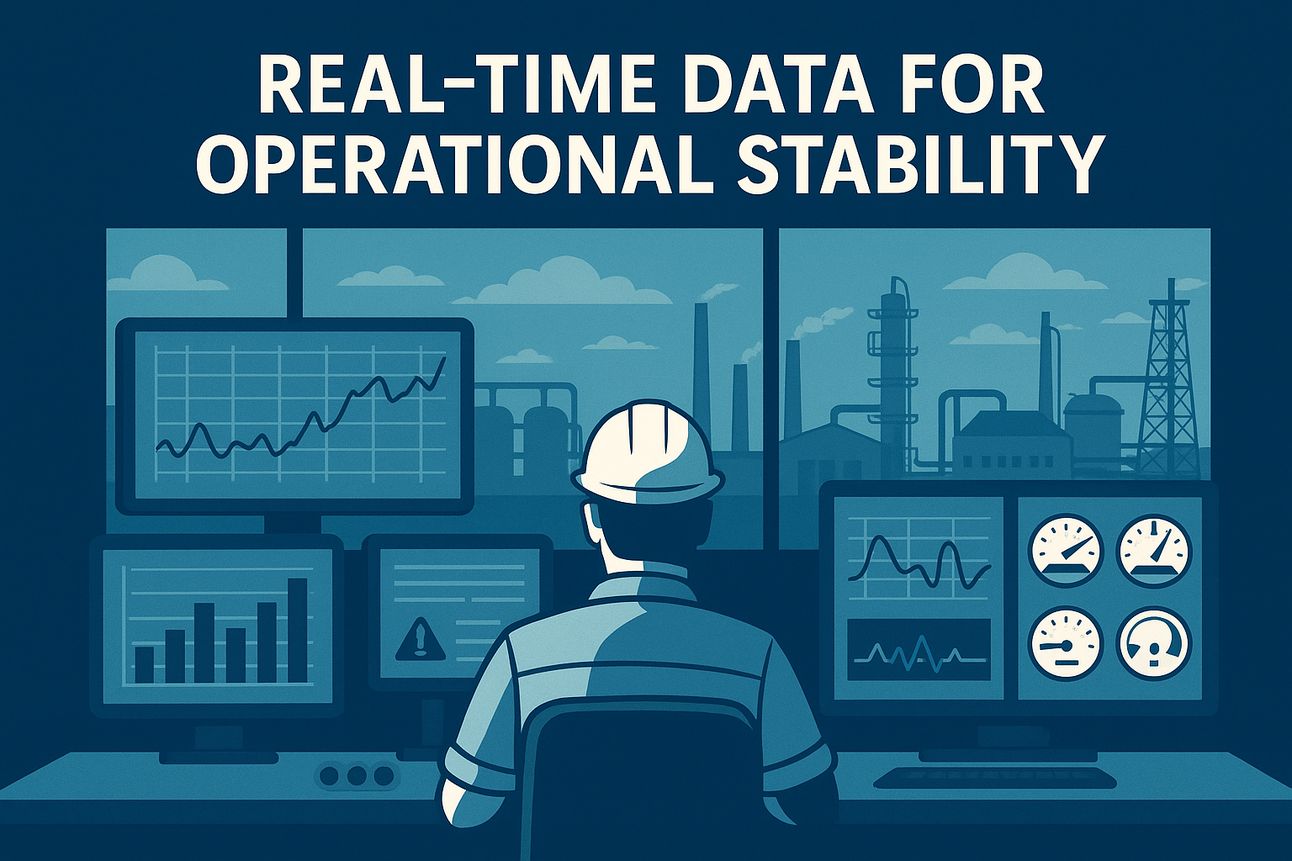
Real-Time Data for Operational Stability
Continuous reporting of the equipment condition supports rapid response to operational challenges, maintaining system stability and performance. Data should be collected periodically throughout the day, multiple times, to support real-time reporting. If there is an anomaly in the data, take more frequent and additional readings until you reach a stable point, allowing you to make the most effective decision. After that, it would be best to return to the regular frequency of data collection.
Flexible Supply Chains for Maintenance Continuity

Flexible Supply Chains for Maintenance Continuity
Agile supply chain strategies ensure maintenance operations remain uninterrupted, bolstering resilience during disruptions.
Why Flexibility Beats Forecasting
Intelligent Risk Prioritization for System Reliability
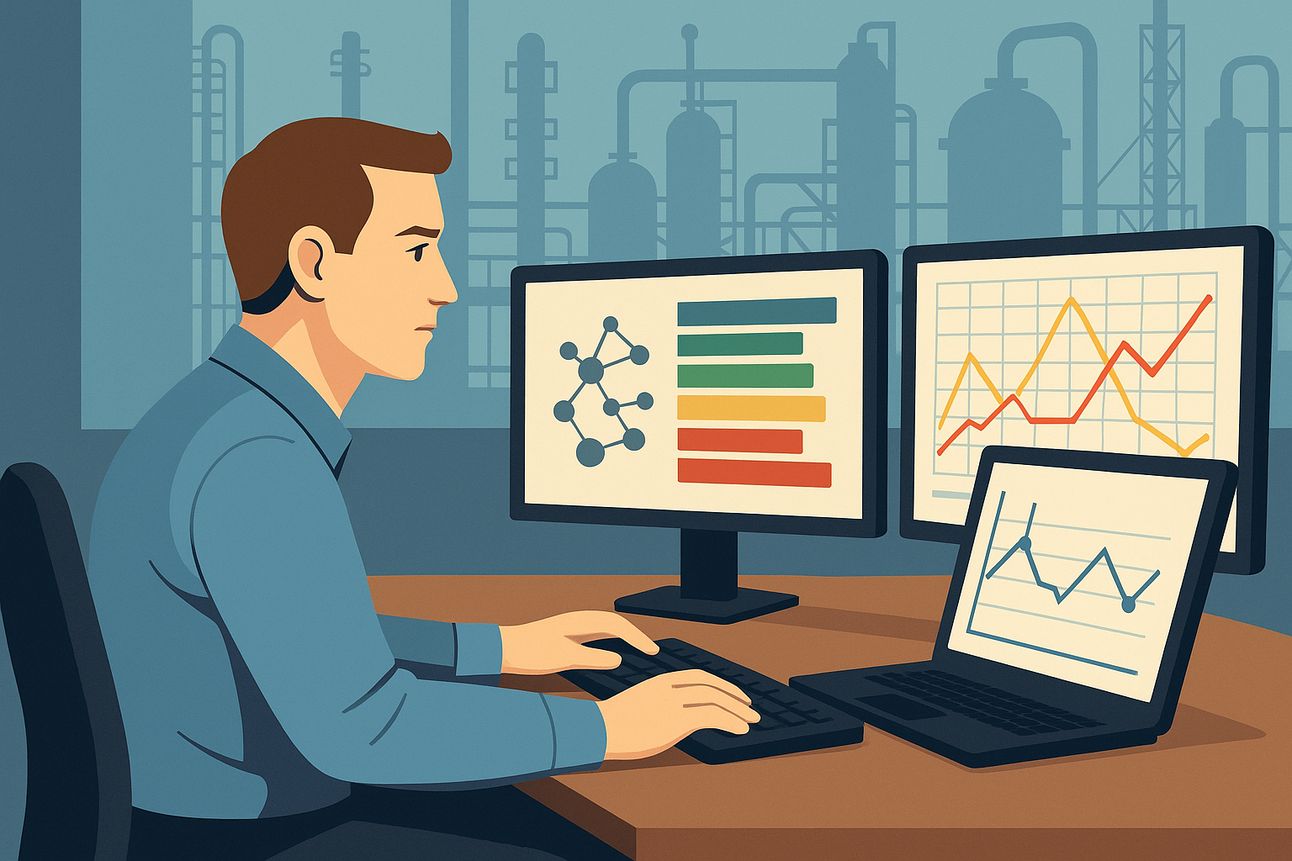
Intelligent Risk Prioritization for System Reliability
Smart algorithms identify and prioritize critical risks, optimizing maintenance efforts to ensure consistent operational reliability.
Too Many Risks, Too Little Time
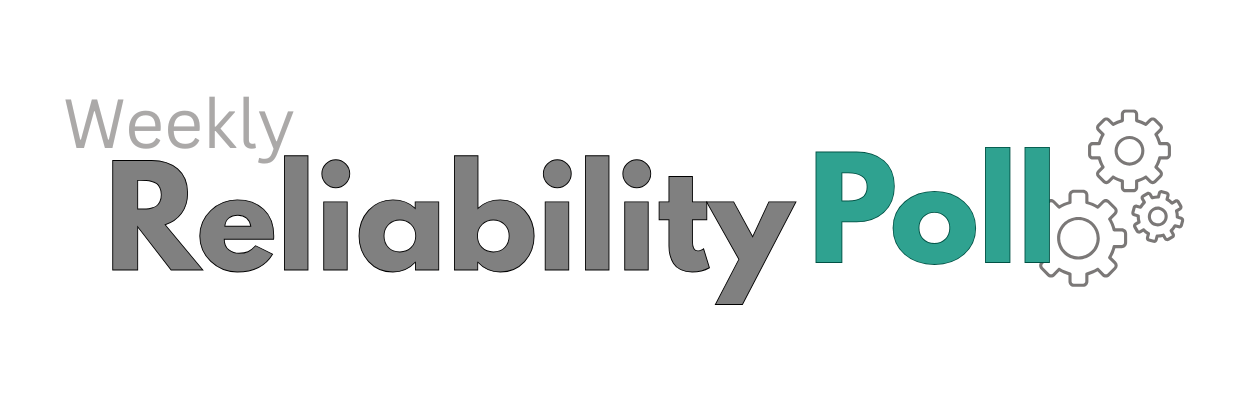
Please answer a brief question and we will share the insights in next week.
From last week, the week of July 1st, your most common reliability challenge was: Insufficient maintenance budget
Do your critical assets have risk profiles? |
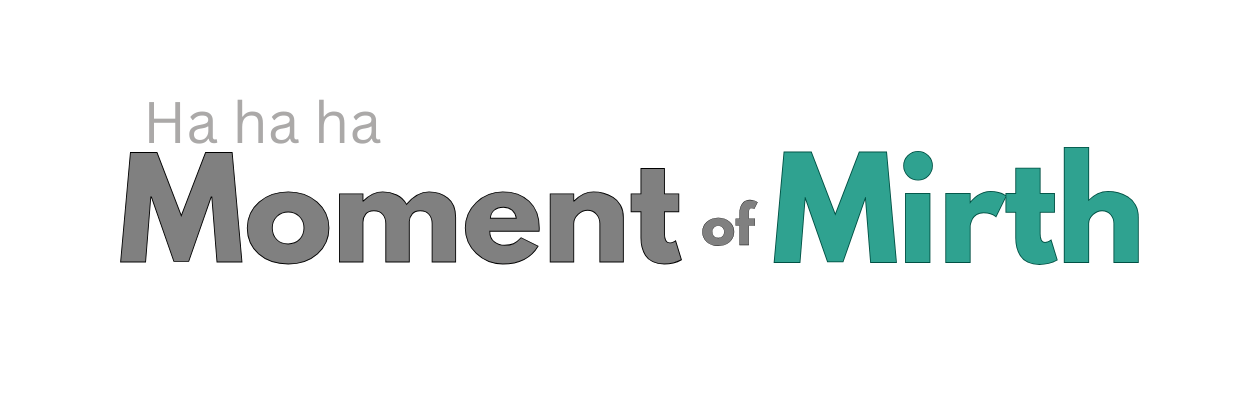
Real-world ridiculousness (or close enough) from the front lines of reliability
"The $0.50 Bolt That Cost $50,000"
At a well-known food & beverage plant, the maintenance team ordered what seemed like a basic M16 bolt to fix a small gearbox housing. Procurement, moving fast, sourced a "close match" from a non-approved vendor. It fit — for a week.
Then came corrosion. Then came the gearbox teardown. Then came three days of downtime, a production halt, and some very quiet finger-pointing.
Lesson learned (and added to the CMMS):
"Always verify specs with the reliability engineer."
Now that bolt sits on a shelf with a tag that reads:
“Legacy part – for storytelling purposes only.”
Source: Hamiltonian Systems. (2025, July 8). Moment of mirth: The $0.50 bolt that cost $50,000 [Anecdote based on conversations with reliability engineers]. Reliability Edge.
This newsletter provides best practices, strategies, techniques, insights and data from our ongoing research in short, concise articles.
By incorporating these tips and techniques into your routine, you can cultivate a operations that flourish throughout the year.
Until next time!